Produktionsplanung und -steuerung – Verlässlich dank KI
17.02.2023 Gerade im Maschinen- und Anlagenbau sind Produktionsabläufe häufig komplex. Durchlaufzeiten und Liefertermine können oft nur geschätzt werden. Mit Methoden der Künstlichen Intelligenz möchte Prof. Dr.-Ing. Matthias Schmidt für mehr Termintreue sorgen.
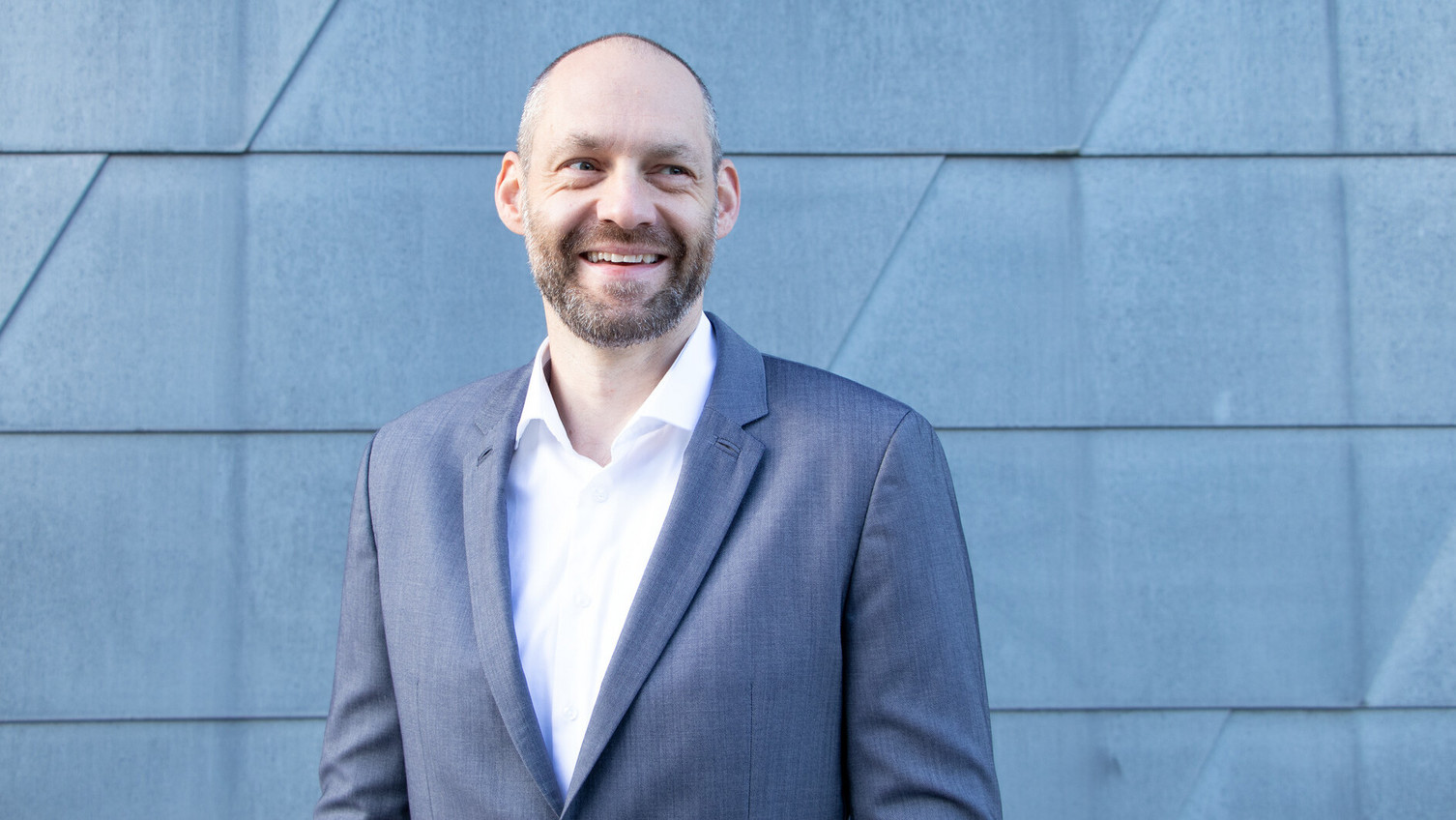
Fertigt ein Unternehmen nicht in Serie, sondern stellt Einzelteile oder Kleinserien her, sind Lieferzeiten oft nicht gut planbar: Eine Firma erhält beispielsweise den Auftrag, eine komplexe Produktionsanlage herzustellen. Für den Bau sind verschiedene Arbeitsschritte nötig wie Metallbearbeitungsprozesse in der Vorfertigung und komplexe Assemblierungsprozesse in der Endmontage. Oft sind einzelne Arbeitssysteme während des Auftragsdurchlaufs durch andere Aufträge blockiert, der externe Lackierer beispielsweise hat selbst ein volles Auftragsbuch oder die Fachkraft an der Fräsmaschine ist krank. Es gibt weit mehr Beispiele, die den Arbeitsablauf bremsen können. Für den Auftraggeber, der die Produktionsanlage selbst in seinem Betrieb braucht, heißt es dann: warten. „Plandurchlaufzeiten werden in der Praxis oft mit groben Faustformeln auf der Basis von Erfahrungswerten geschätzt“, sagt Dr.-Ing. Matthias Schmidt, Professor für Produktionsmanagement.
Der Forscher möchte mit Hilfe von Künstlicher Intelligenz Plandurchlaufzeiten, also die Zeit vom Auftrag bis zur Lieferung, verlässlicher vorhersagen. Gemeinsam mit seinem Team analysiert er Daten von sechs mittelständischen Unternehmen und sucht Muster: Was sind die wesentlichen Parameter, die sich signifikant auf die Plandurchlaufzeiten auswirken? „Nicht immer haben alle Variablen tatsächlich Einfluss auf die Durchlaufzeit“, erklärt Matthias Schmidt. Mithilfe von Methoden der KI wie etwa neuronale Netze werden komplexe Arbeitsabläufe analysiert, die teilweise mehr als 30 Schritte enthalten. Zum Ende des Forschungsprojektes sollen die Unternehmen eine alltagstaugliche Methode an die Hand bekommen, mit denen sie Plandurchlaufzeiten genauer vorhersagen können.
Die Deutsche Forschungsgemeinschaft (DFG) fördert „Quantifizierung zentraler Inputfaktoren zur Bestimmung von Plandurchlaufzeiten in der Werkstattfertigung“ mit rund 130 000 Euro.